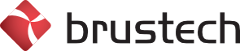
Decontamination and cleaning of petrochemical installations and equipment.
Decontamination and cleaning of petrochemical installations and equipment is essential during their lifespan, and the time it takes to complete such works is undoubtedly an important issue. Accordingly , Brustech has developed a technology which significantly shortens the process.
This allows not only repair works or inspections to start earlier, but also speed up whole production process, thereby minimizing down time losses, and thus providing an increase in productivity, which – in the end – leads to improving financial results.
Another advantage of the technology proposed by Brustech is safety. This is because it has been developed in order to simultaneously eliminate the risk of damage to the equipment or installations, as well as to ensure the safety of the workers.
An important benefit of the technology proposed by Brustech is that it allows removal of harmful gases such as hydrogen sulphide, benzene, hydrocarbon vapours etc., as well as polymer residues. In addition, thanks to this technology, hydrocarbon contaminants are subjected to emulsification, acids are neutralized, pyrophoric deposits deactivated and any other residue containing harmful substances is dissolved.
Decontamination and cleaning technology can be used on a large range of equipment and installations such as:
- Distillation Towers
- TDI / TDA Installations
- Hyrdrotreaters
- Coker Units
- Fluid Catalytic Cracking Installations
- Isolation Tanks
- Claus Plants
- PX / PTA Installations
- Hydrocracking Installations
- Amination Installations
- Catalytic Reforming Units
- Reforming Units
- Amine Absorbers
- Amine Regenerators
- Ammonia Separators
- Hydrodesulfurization Units